Because it\'s cold outside in the garage/workshop, I decided to work on a components that I could do inside. I decided to do some work on the BASE PLATE. The BASE PLATE bolts onto the top of the TOP COVER to allow the BROADWELL DRUM to be fitted instead of using a stick magazine.
The BASE PLATE was one of the components that I decided to cast. In hind sight......
This is the underside of the BASE PLATE. In this photo you can see the sprue where it was cast (I\'ve already cut it off and placed it back in position for the photo). You can also see where holes should have been cast. Most of them are almost all the way through, but one of them you can only just locate.
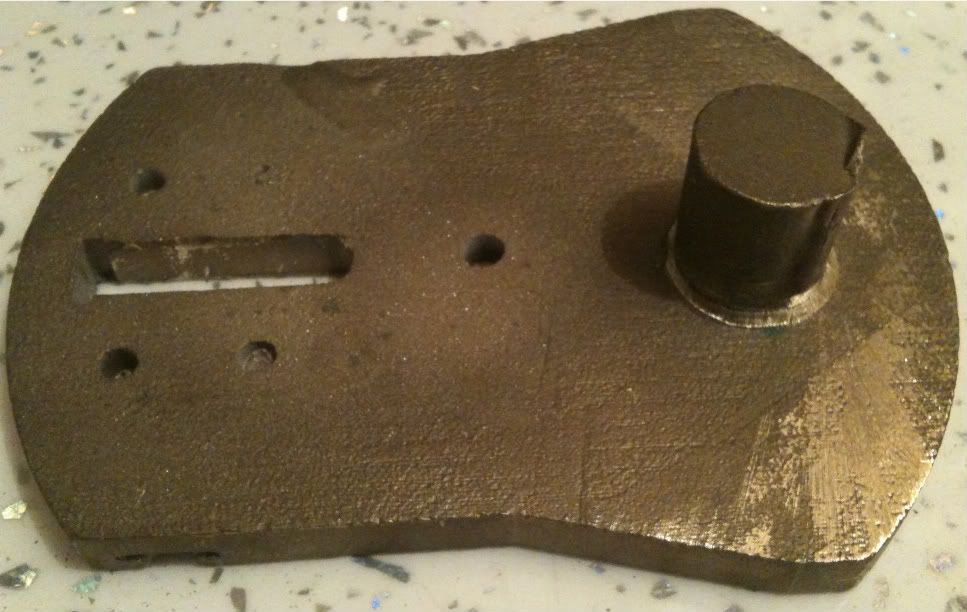
This is the top of the BASE PLATE. In this photo you can see the two slots that the KEY,SHORT and KEY,LONG slide into. Well, they should slide in. The slot that the round of ammunition drops through is very well formed, but the flashing disguises that.
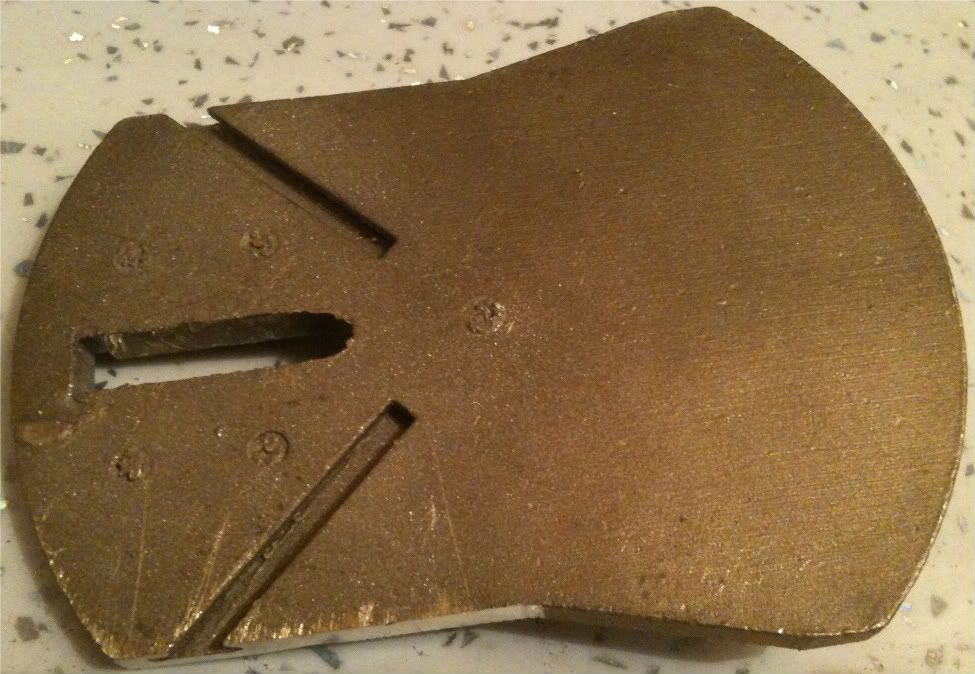
I\'ve cleaned up the BASE PLATE and KEY,LONG and they now fit together nicely. The surface looks awful, but is very flat and has been finished with 150 grit so far. I\'ve not cleaned up the hole that the round of ammunition drops through as once the BASE PLATE is bolted to the TOP COVER there may be a slight mismatch. I\'ll finish the hole off once both parts are bolted together.
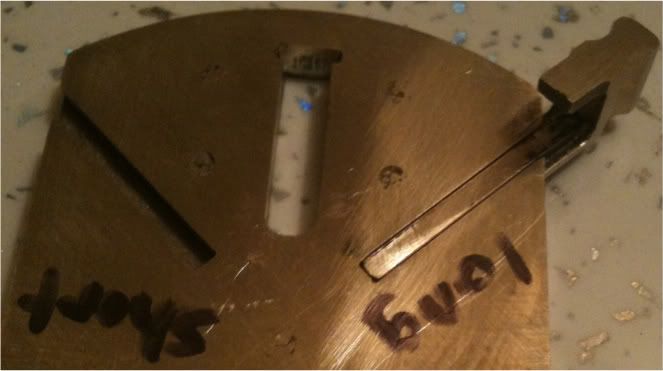
Here\'s the BASE PLATE and the KEY,LONG. You can see that the end of the KEY,LONG is rounded, whereas the end of the slot is square. I\'m not sure I like this so may modify one or the other. On the flip side, this joint wont be seen once the BROADWELL DRUM is in place.
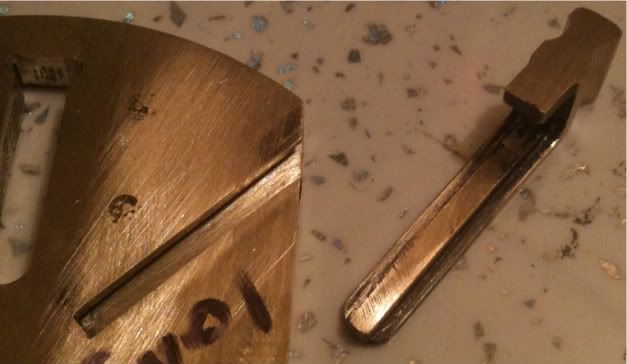
Here you can see the cross section of the two parts.
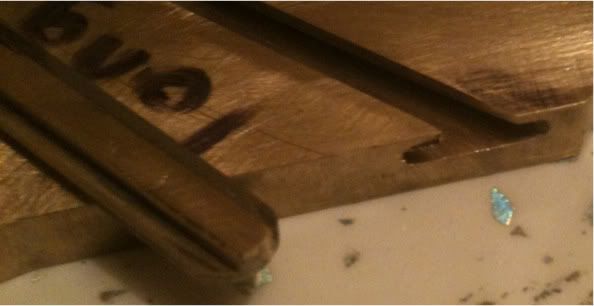
How did I get the two parts to fit? The slot was nowhere near as well formed as I\'d hoped. I used a small needle file, a small dremmel with a modified cutter and lots of patience. In hind sight, I should have bit the bullet and machined this part from solid. I decided to cast it as I knew I wouldn\'t have access to a mill when I came to machine it. As it happens, I\'ve got a big pillar drill and a compond table so I could well have machined it at home. I\'m considering machining some of my other parts that I already have castings for, since machining a casting is a nightmare and very hard on cutters because of the ceramic on the surface.
I\'ll do a write up on using cast parts in a fresh thread and put a link to it here: