I had a lot of problems with turing my barrels, so thought I\'d post a write up on here about how I did them.
I bought my barrels as blanks that were something like 500mm long and 25mm diameter.
The first thing I did was to chop them to slightly over length at about 420mm.
To skin them down to the required OD of 12mm I clamped them in the lathe with just over half hanging out of the chuck. The loose end was held in a revolving center.
I then turned the barrel around and skinned down the other end to 12mm as well.
I wanted to turn the detail on the breach end of the barrel which would eventually be threaded so did this at this stage.
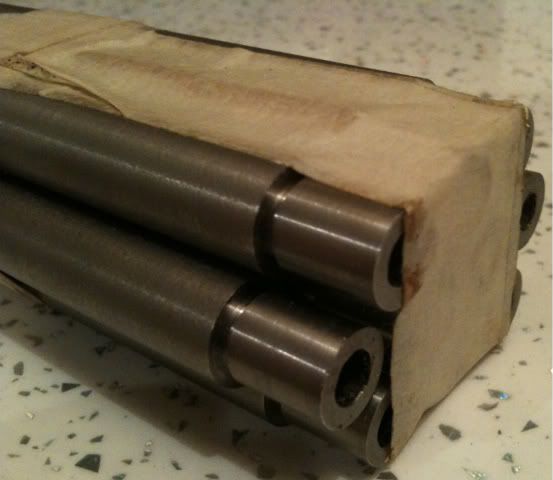
I also machined the hexagon profile on the muzzle end of the barrels at this stage.
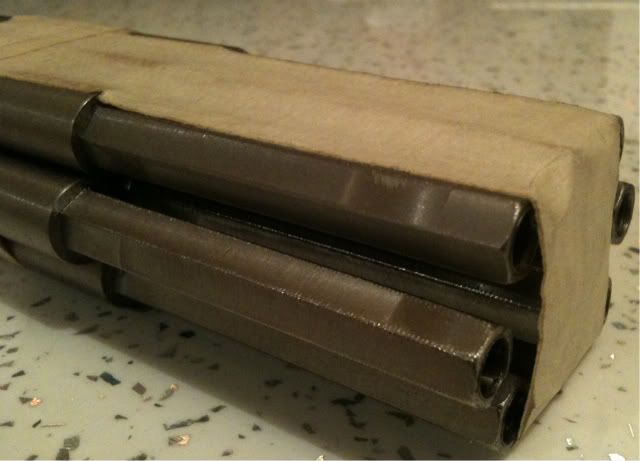
The next stage was to turn the taper on the barrels. I decided to offset the tailstock to do the tapers. I moved the tailstock towards me which meant when I parrallel turned, I ended up with a tapered barrel. I wrapped two layers of masking tape around area that would eventually be threaded and placed this into the chuck jaws.
At the muzzle end, I\'d turned up a brass dowel that was snug fit in the barrel. I placed this in the tailstock chuck and oiled it up before sliding it into the barrel. A rotating center would have been ideal.
When I spun the barrels up in the lathe, I found that they were not perfectly aligned since I had thinned them in two seperate operations previously. Because I was cutting a taper, the fixed steady and the moving steady weren\'t really ideal.
I found that I could make a cut with no chatter if I had an rpm of 200, a 0.2mm/rev feed and a 0.1mm cut. Each cut along the length of the barrel takes 24 minutes though. I\'ve never had to do such a ridiculous cut!! I managed to get the first taper done on one barrel in 6 hours.
I decided to use the fixed steady from this point on.
I cut two true \'bearing\' surfaces for the fixed steady to run on using the 200rpm / 0.2mm/rev / 0.1mm cut.
I then placed the fixed steady in the far right \'bearing\' surface and was able to cut the barrel using a 500rpm / 0.8mm/rev / 0.2mm cut to within 0.6mm of final taper diameter
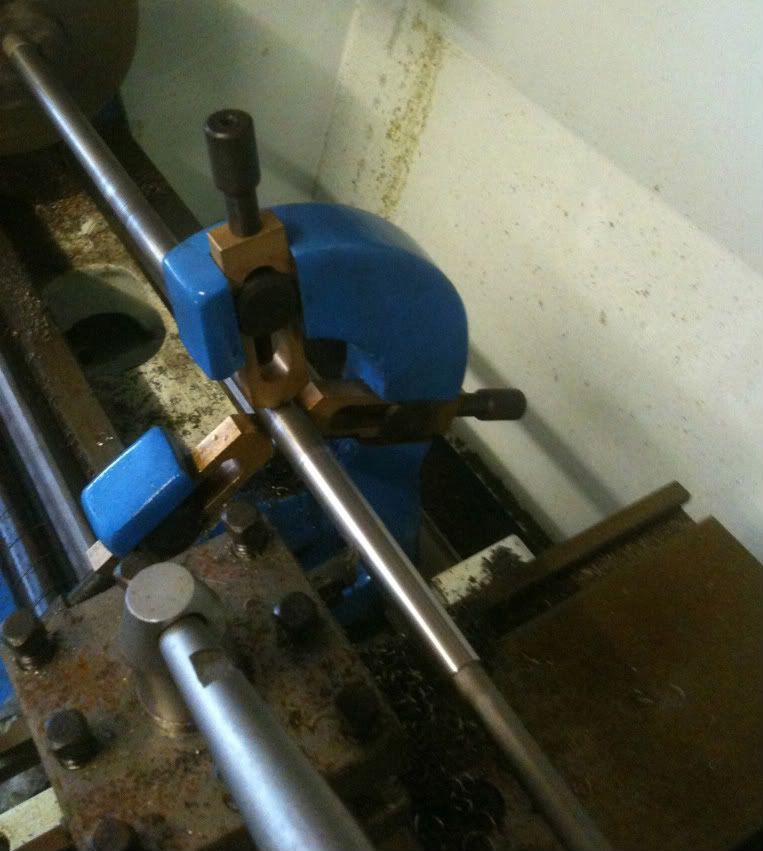
I moved the steady to the left \'bearing\' surface and again turned down to within 0.6mm of final taper diameter.
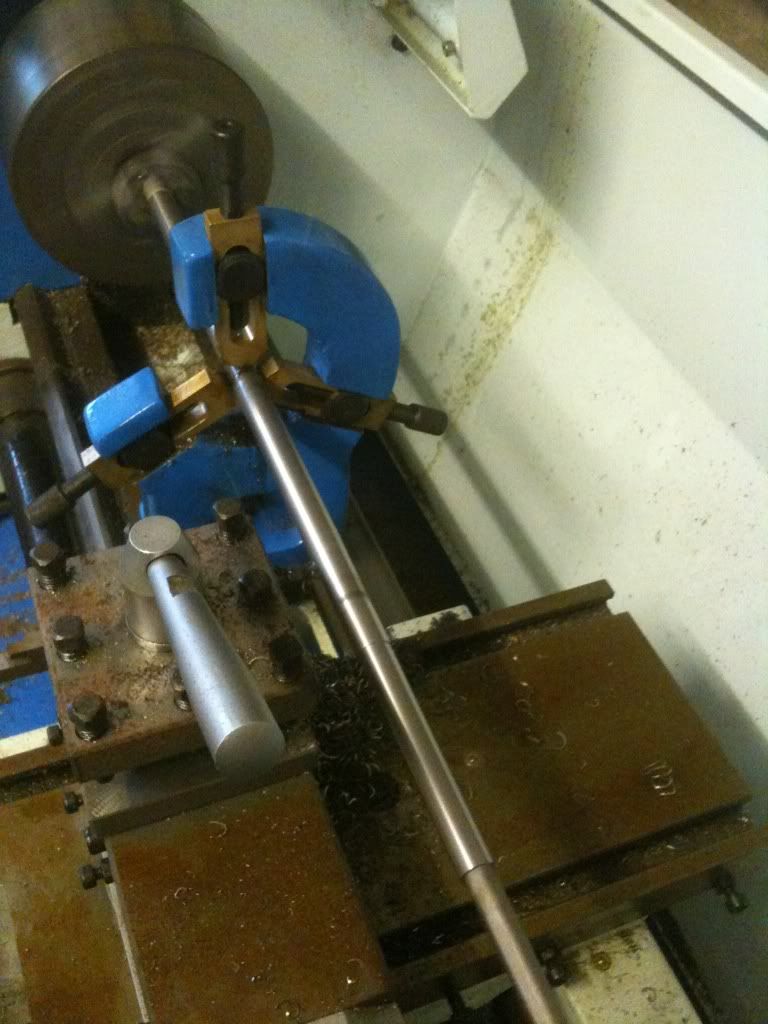
I then removed the fixed steady and cut the remainder of the barrel using the 200rpm / 0.2mm/rev / 0.1mm cut. There were only two cuts needed about 100mm long.
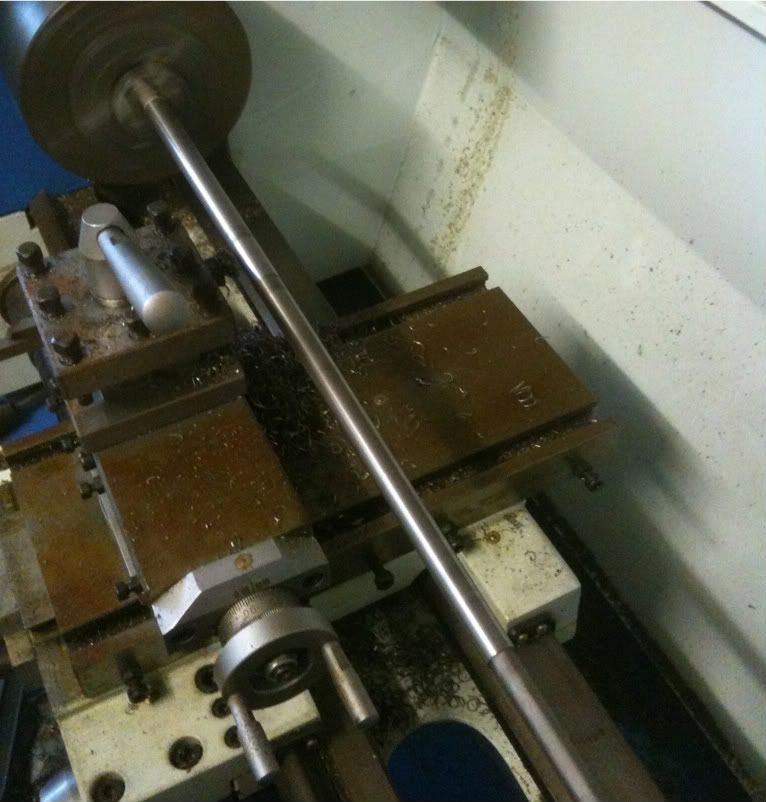
I then did 6 cuts using the 200rpm / 0.2mm/rev / 0.1mm cut for the whole length of the barrel which I\'d smeared in oil. (No coolant on my lathe)
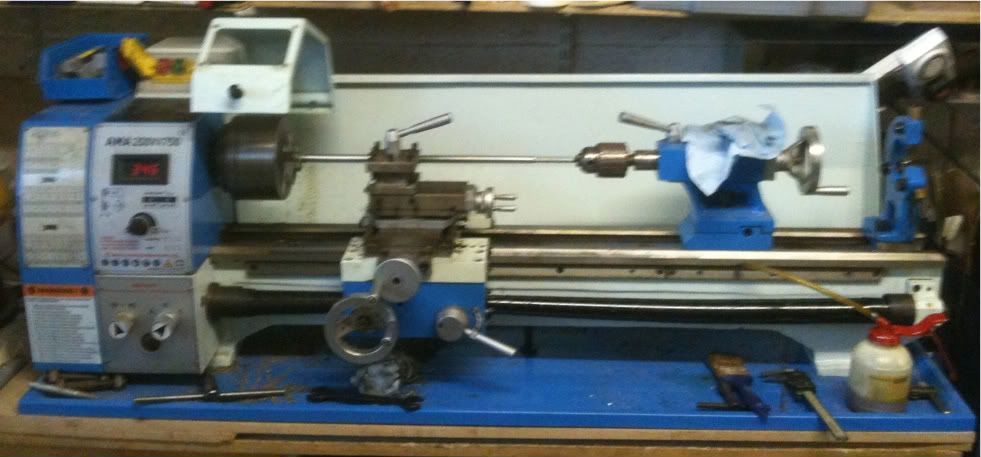
I finished my second barrel in about 3.5 hours which is a large improvement.
Normally I\'d be very annoyed at having to stand watching a lathe for 24 minutes at a time, but I\'ve got so many other parts to make, I\'m just spending the 24 minutes working on other parts on the bench next to the lathe.
I tried a few different methods of cutting the tapers but all were a nightmare to do. The process listed above worked well. I hope this helps someone.